While it would certainly be impossible to cover every troubleshooting situation for every single product packaging device in manufacturing, there are some persisting issues that have actually arisen over the years. Several of the more usual problems do not always have a noticeable resolution, though even more times than not a basic repair will certainly have the equipment running manufacturing regularly and accurately quickly whatsoever. Below are a few of those common problems, in addition to the regular repairs.
- Irregular Loading
Various filling up equipment, of course, make use of various filling principles and different kinds of nozzles. So inconsistent filling can originate from different resources depending upon the sort of fluid filler being used on a packaging line. Generally, nevertheless, the source is commonly either an inaccurate setup of the loading machine or wears parts that require to be changed.
Throughout the establishment of the bottle filler, nozzles must be positioned appropriately over the bottles. Some nozzles, such as those found on an overflow filler, will dive into a bottle and also develop a seal. The compression on these nozzles needs to also be set properly to accomplish consistent, level fills. Operators experiencing inconsistent dental filling should initially examine the physical establishment of the devices, guaranteeing nozzles are associated with the bottles and diving correctly. A power conveyor system will typically relocate bottles right into and out of the fill area also, with the help of an indexing system, such as entrance and also exit pins, a celebrity wheel, or a few other sorts of systems. The driver ought to check the guide rails to guarantee bottles are consistently aligning in the right placement, in addition to the indexing system to verify that containers are maintained while in the file location.
Automatic loading devices will normally be managed by a PLC, accessed using a touchscreen interface found on the control panel of the machinery. The operator interface will enable the user to establish fill times along with hold-up and duration times for components such as the head dive, pump, indexing as well as more. Normally these makers will come with settings for individual bottles pre-set on a recipe screen. Irregular fills up can develop from having wrong fill times, hold-up times, or period times, or from going into the wrong recipe for the product and also the bottle being run. The operator ought to likewise check to guarantee all the settings are right. As a side note, it is always a great idea to maintain a hard copy of all times and also setups in case of damages to the PLC from an extreme atmosphere, a power blackout, or various other unexpected situations.
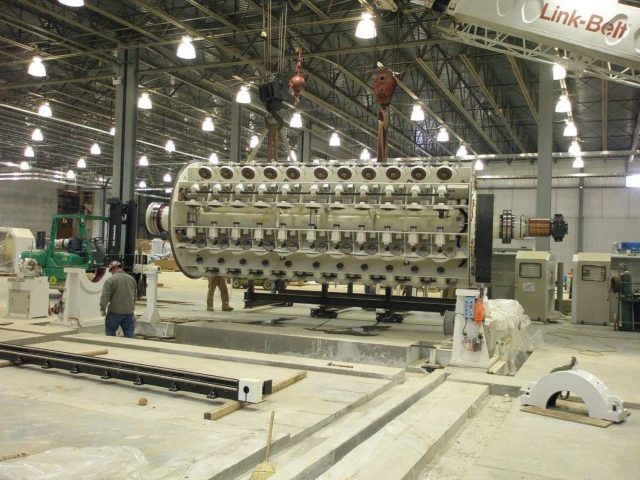
When these checks have been finished, if irregular fills up continue, any worn parts located on the packaging maker should be evaluated and replaced if needed. Numerous nozzles will certainly consist of O-rings or seals that will, with time, require replacement. These O-rings, seals, and also similar elements can allow air right into the product path at numerous points, causing inconsistent fills. In fact, drivers should additionally evaluate as well as tighten up hose clamps linking tubes to the maker along the product path, as something as straightforward as a small amount of air entering the path at the tubing can create a variance. Going through these easy checks will lead a driver to the solutions for troublesome fills up a bulk of the time.
- Inconsistent Capping
When a packaging line is filling regularly, the last thing a driver wishes to deal with is irregular topping, which can cause cross threads, loosened caps, or difficulty opening tight covers. Just like the filling up devices, topping devices will differ based upon the sort of cap and also seal being used. Nonetheless, some straightforward inspection of set up and use parts will once more typically lead to the remedy.
The topping apparatus, whether spindle wheels, a chuck head, snap-on belt, or another device, should be correctly put to accurately as well as continually seal containers. The driver needs to first check the topping apparatus to make sure that caps are being called at the proper position to develop this trusted and constant seal. The change will generally include basic tweaks to the height and also size of the apparatus, and also some experimentation may be included. If it shows up that the topping device is properly situated, attention should be reported to any kind of components used to support the bottle and also the cap. Gripper belts, overview rails, cap tongues, and cap stabilizer bars will all be used to make certain proper sealing. If bottles or caps are not maintained, the movement can play havoc on the capping procedure. Check these maintaining components to ensure containers and caps are safe throughout the sealing procedure.
Covering device wear parts are typically contact components. Spindle wheels rotate down screw-on caps, snap-on belts apply pressure to break on caps. Gripper belts contact the bottle to maintain it via the topping process. As these parts wear down, they come to be less efficient. Operators can evaluate the worn parts on their specific bottle capper and make replacements as essential. Again, experiencing these simple actions will resolve inconsistent covering more times than not.
- Container Tipping as well as Spills
The trick to fixing container tipping as well as spill concerns is to situate the source. If the pointers or spills are taking place at a solitary place, a driver might require to go back to the established inspections explained above. A poorly positioned indexing system on loading equipment, for instance, might result in tipping bottles. Wrong fill times may result in spills. Gripper belts pressing too firmly on a bottle might push an item out of that bottle prior to a cap being properly tightened up at the covering as well as sealing station. If bottle tipping or spills can be pinpointed to a single maker or area, check the device and make adjustments as needed.
If relatively arbitrary tips or spills happen along the packaging line, the transfer system, usually a power conveyor system, might be the problem. The driver ought to evaluate the conveyor belting, in addition to any type of transfer areas, for damage. A fracture or missing piece of belt can cause containers to become unpredictable while moving along the conveyor. Damage to a transfer plate in between conveyors may cause bottles to jump or tip too. Finally, the operator can validate that the conveyor rates are appropriate and also regular along the product packaging line. If one or more conveyors have actually unintentionally been slowed down or accelerated, the exchange from one rate to another may cause tipping or spraying and also spills.
- Maker Elements and PLC Setups
Every now and then, the packaging process in its entirety will certainly work properly, but a solitary element of equipment will certainly not carry out. As an example, drip trays and head dives on loading machines prevail against wrongdoers. Generally, either set in the PLC will certainly solve such problems. The driver user interfaces for the PLC will certainly generally include a Guidebook Toggle Display, made use of to control specific components of the product packaging machinery during the establishment of the equipment or while performing maintenance. The drip tray can be withdrawn under the Handbook Toggle screen to maintain it off the beaten track during establishment or maintenance. Nevertheless, if the setup is not gone back to the Vehicle before beginning manufacturing, the drip tray will continue to be retracted. The initial setups to check when a single component is not working appropriately are those located in the Guidebook Toggle display of the operator user interface, set the element to Vehicle if it is not currently in this position.
The Establish display on the driver interface likewise includes settings for sure parts of the tools. For instance, vision systems on packaging equipment can typically be set to review typically or inverted (depending upon the type of container being used, transparent versus non-transparent as an example). If vision systems or other parts on a packaging system are not working appropriately, the operator needs to see the Set-Up display to make sure the element is enabled to function correctly with the packaging and item.
While these simple fixes will certainly solve more problems than not, there are constantly those unusual events when a service averts uncover. As packaging tools are generally produced for the certain project for which it is being made use, the driver must constantly have the producer to draw on. So if all else stops working, pick up the phone as well as talk to a Product packaging Specialist to get production back to the smooth, trusted, and consistent process that is wanted. Find a Hampshire bulldozer hire by going to this website.